Jednym z robotów, nad którym pracujemy w ramach projektu aRMoRS, jest hexabot, którego planowanymi zadaniami jest zwiad oraz mapowanie przestrzeni. Zaprojektowanie robota o takiej kinematyce i zastosowaniu nie jest prostym zadaniem – wymaga między innymi odpowiedniego balansu rozłożenia masy, wielkości, siły poszczególnych kończyn robota. Mimo przyłożenia dużej wagi do wyżej wymienionych aspektów nie jest łatwym pozbyć się wszystkich pomyłek w fazie projektowej. Powstaje potrzeba przenieść koncepcje do świata rzeczywistego, aby móc w pełni sprawdzić zaprojektowane komponenty.
Przejście z fazy projektowej do rzeczywistego prototypu obarczone jest w swoje własne problemy. Jest to etap, w którym nasz robot zaczyna nabierać już konkretnego kształtu. Każda pomyłka czy niedociągnięcie na poziomie obliczeń i/lub modelowania może opóźnić projekt i przynieść ze sobą dodatkowe koszty. Sprawy nie ułatwia poziom skomplikowania hexabotów oraz konieczność interdyscyplinarnej wiedzy z zakresu elektroniki, automatyki i mechaniki. Pociąga to za sobą konieczność sprawnej komunikacji pomiędzy zespołami jak i wewnątrz nich.
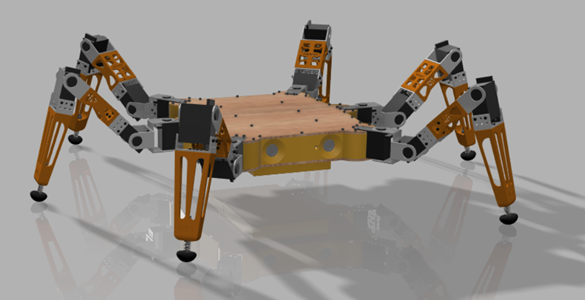
Na szczęście stosując technologię druku 3d zminimalizujemy skutki ewentualnych pomyłek i znacząco skracamy czas ,,od projektu do prototypu “. Dzięki drukowaniu poszczególnych elementów możemy nie tylko przyspieszyć pracę nad pierwszym prototypem, ale również ograniczyć koszty jego wykonania i w krótkim czasie przejść do testowania jego kluczowych cech. Idealnym przykładem działania tego procesu jest wykonanie przez nas prototypu elementów jednej z nóg robota (są to pomarańczowe elementy widoczne na wizualizacji, na Rys. 1.). Na wykonanie wstępnych modeli i następnie ich wydruk przeznaczyliśmy trzy dni. Tak szybki proces wytworzenia pozwolił na przetestowanie elementów na najbliższym spotkaniu zespołów projektowych i szybką weryfikację ich funkcjonalności. Jak się okazało, dłuższy element nóżki był bardzo podatny na skręcanie. Nie wykrycie tego problemu we wczesnym etapie projektowania mogłoby przysporzyć nam dużym problemów przy testowaniu gotowego prototypu. Uniknęliśmy dzięki temu zbędnych kosztów oraz zwiększenia nakładu zadań związanych z retrospektywnym szukaniem usterki.
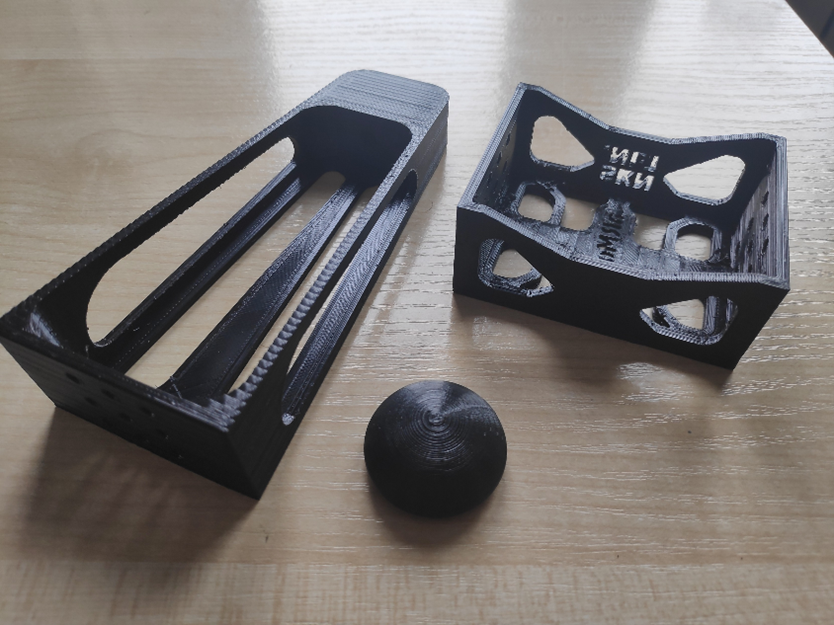
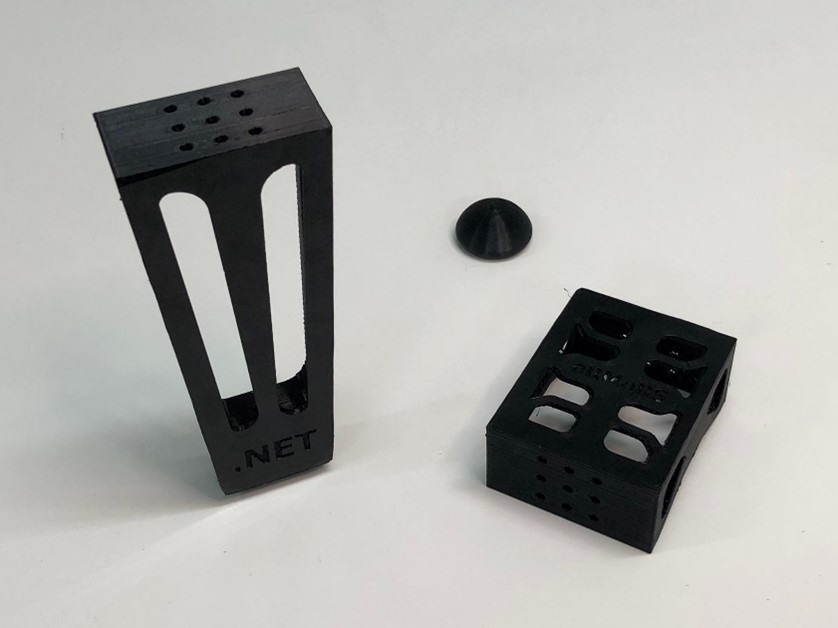
Projektując elementy pod wykonanie ich na drukarce 3d należy pamiętać, że odpowiedni kształt modelu może znacząco usprawnić proces drukowania, oszczędzając czas oraz materiał. Istnieją dwie podstawowe zasady projektowe znacząco ułatwiające wydruk. Po pierwsze, jeśli to możliwe staramy się, aby jedna z powierzchni modelu była płaska. Zwiększy to powierzchnię styku detalu ze stołem drukarki, a co za tym idzie również przyczepność eliminując potrzebę stosowania tratwy (ang. raft) oraz podpór podtrzymujących drukowany model. Drugą zasadą jest ograniczenie ilości nawisów lub zmniejszenie ich nachylenia poniżej 45° (najlepiej do ok 40°). Każdy nawis nachylony pod większym kątem wymaga podparcia przez strukturę zwaną wspornikiem (ang. support). Każdy wspornik zwiększa czas druku, zużywa pewną ilość filamentu, a co gorsze po zakończeniu wydruku wymaga ręcznego usunięcia, co dodatkowo wydłuża czas wykonania modelu oraz pozostawia po sobie mało estetycznie wyglądającą powierzchnie.
Pomimo skomplikowanej natury projektowania modeli pod druk 3d ma on wiele nietypowych zalet. Dzięki możliwości regulacji stopnia oraz kształtu wypełnienia, ilości zewnętrznych ścianek i innych parametrów możemy płynnie wpływać wytrzymałość danych modeli, ich sztywność oraz masę. Druk 3d pozwala uzyskać geometrie trudne lub wręcz niemożliwe do uzyskania innymi technologiami.